“Professional Refinishers: Are You Still Spraying Over Old Junk?
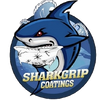
Understanding Common Coating Failures in the Bathtub Refinishing Industry
And How to Determine if You Can Bond Over or Must Strip First
Introduction:
In the bathtub refinishing business, what separates seasoned professionals from the rest isn’t just how well they spray—it’s how well they prep and problem-solve. Coating failures are rarely caused by the paint itself but by misapplication, surface incompatibility, or cutting corners during the prep stage. Knowing what failure looks like and what causes it can save your reputation, your profits, and a whole lot of callback grief.
This guide explains the most common coating failures seen in the bathtub, tile, and countertop refinishing industry, followed by a step-by-step method to evaluate when a tie-coat system is appropriate versus when full stripping is mandatory.
1. Cracking
What It Looks Like: Linear fractures or networks of cracks that start small and grow with time, often radiating from corners or seams.
Why It Happens:
- Overly thick topcoat or under-catalyzed mix.
- Incompatible layers—e.g., urethane over an unstable previous coating.
- Thermal cycling stress (hot water + cool air).
- Applying new coatings over old generic coatings not designed for tubs.
Industry Insight: Cracking is common when someone uses off-the-shelf coatings like Cardinal, Sherwin-Williams, or PPG industrial urethanes, thinking “urethane is urethane.” While good coatings for what they’re engineered for, most have not been specifically made for this industry. These systems aren't engineered to flex with porcelain or survive constant wet/dry and heat/cool cycles. Even worse if the coating underneath is already failing. Many refinishers often place most of their focus on hardness. However, equal emphasis should be placed on flexibility.
For bathtub refinishing over flexible fiberglass units, especially one-piece tub/shower surrounds or combo units, you're dealing with materials that expand, contract, and even flex under body weight and thermal stress. These units are notorious for micro-movement at the wall base, corners, and floor pan — which is why flexibility and elongation in your coating system is critical.
? Flexible Mandrel Rating: What to Look For
- ASTM D522 rating: 1/8" (3 mm) mandrel bend — PASS without cracking or adhesion loss
- Elongation target (ASTM D638 or similar): 60–100% elongation before failure
? SharkGrip Coatings Application Tip
2. Sagging
What It Looks Like: Drips, runs, or droopy streaks, especially on vertical surfaces like the apron or interior walls of the tub.
Why It Happens:
- Applied too wet or too heavy in one pass.
- Too much reducer or wrong solvent blend for ambient temperature.
- Low air temperature or poor flash-off between coats.
Pro Tips:
- Use the correct viscosity and reducer ratio for your spray setup.
- Allow proper flash time, especially on cooler or humid days.
- Spray verticals with care—light, controlled passes are key.
3. Running and Cissing (Fisheyes)
What They Look Like:
- Running: Streaks or vertical flow lines, leaving thin areas behind.
- Cissing: Coating pulls back in tiny circles or crater-like defects.
Why They Happen:
- Silicone or wax contamination.
- Body oil, shampoo residues, or household cleaners that weren’t fully removed.
- Skipped degreasing or improper prep on plastic, Formica, or fiberglass.
How to Prevent It:
- Always clean with Scumbuster, then follow with SWAT solvent wipe to break down silicone, waxes, and oils.
- For risky substrates, apply Bull Shark Adhesion Promoter before your topcoat.
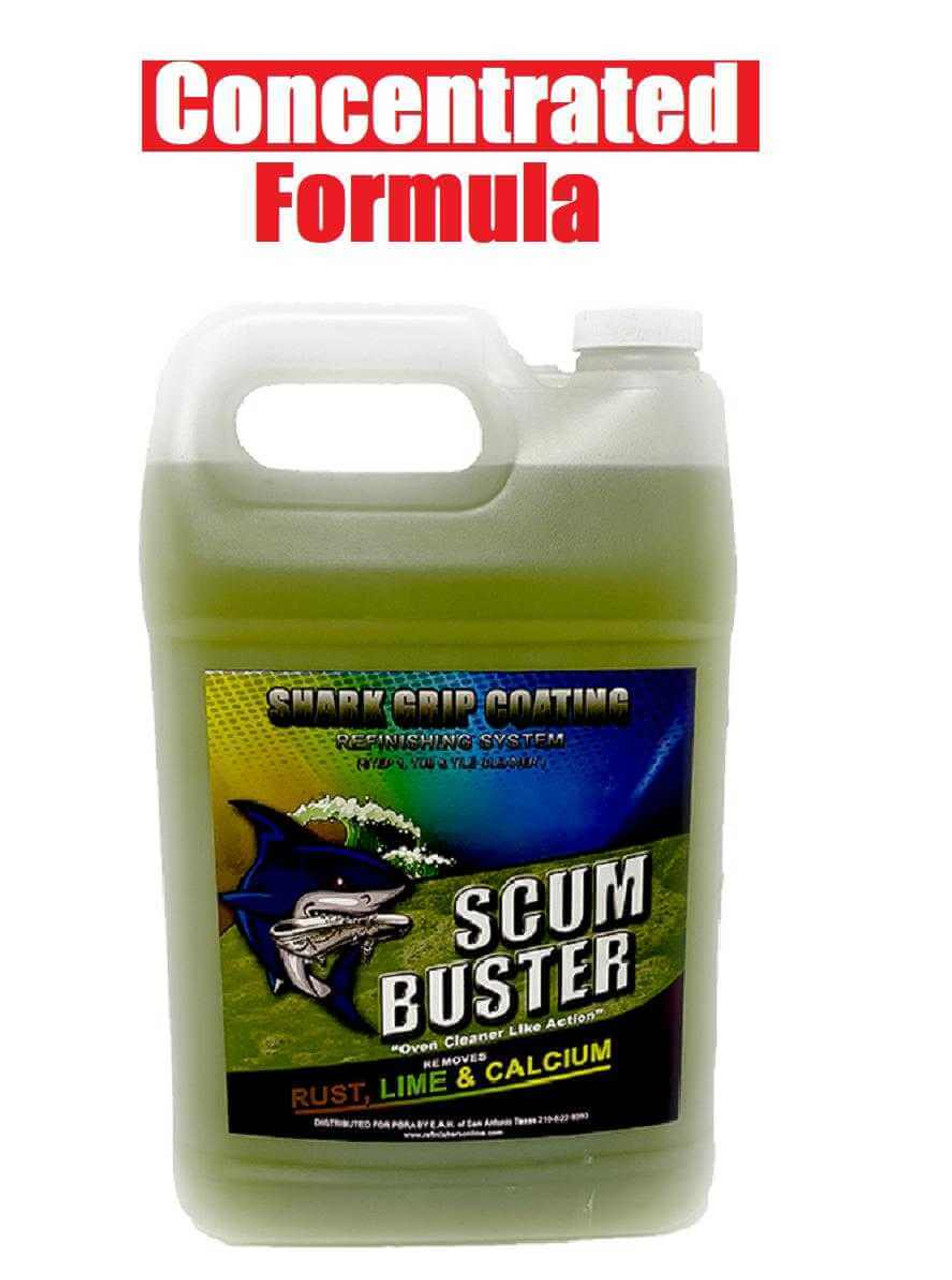
4. Blistering
What It Looks Like: Bubbles under the coating that appear hours or days after spraying—sometimes burst and leave a crater.
Why It Happens:
- Trapped solvents due to excessive film build or poor flash times.
- Moisture under the coating.
- Spraying over a soft or uncured base layer.
Industry Note: This is common when rushing a job or applying new material over a poorly cured DIY kit or multi-layer job. If it’s soft underneath, expect problems.
5. Peeling
What It Looks Like: Entire sheets or chunks of coating lift off, sometimes to bare porcelain or fiberglass.
Why It Happens:
- Skipping silane bonding or scuffing prep.
- Coating over an unknown substrate or consumer-grade product.
- Applying a high-solids urethane over an unprepared glossy surface.
Best Practice: Use Power Bond Silane Coupling Agent on glossy, porcelain, or unknown surfaces. It forms a covalent bond—not just a mechanical one.
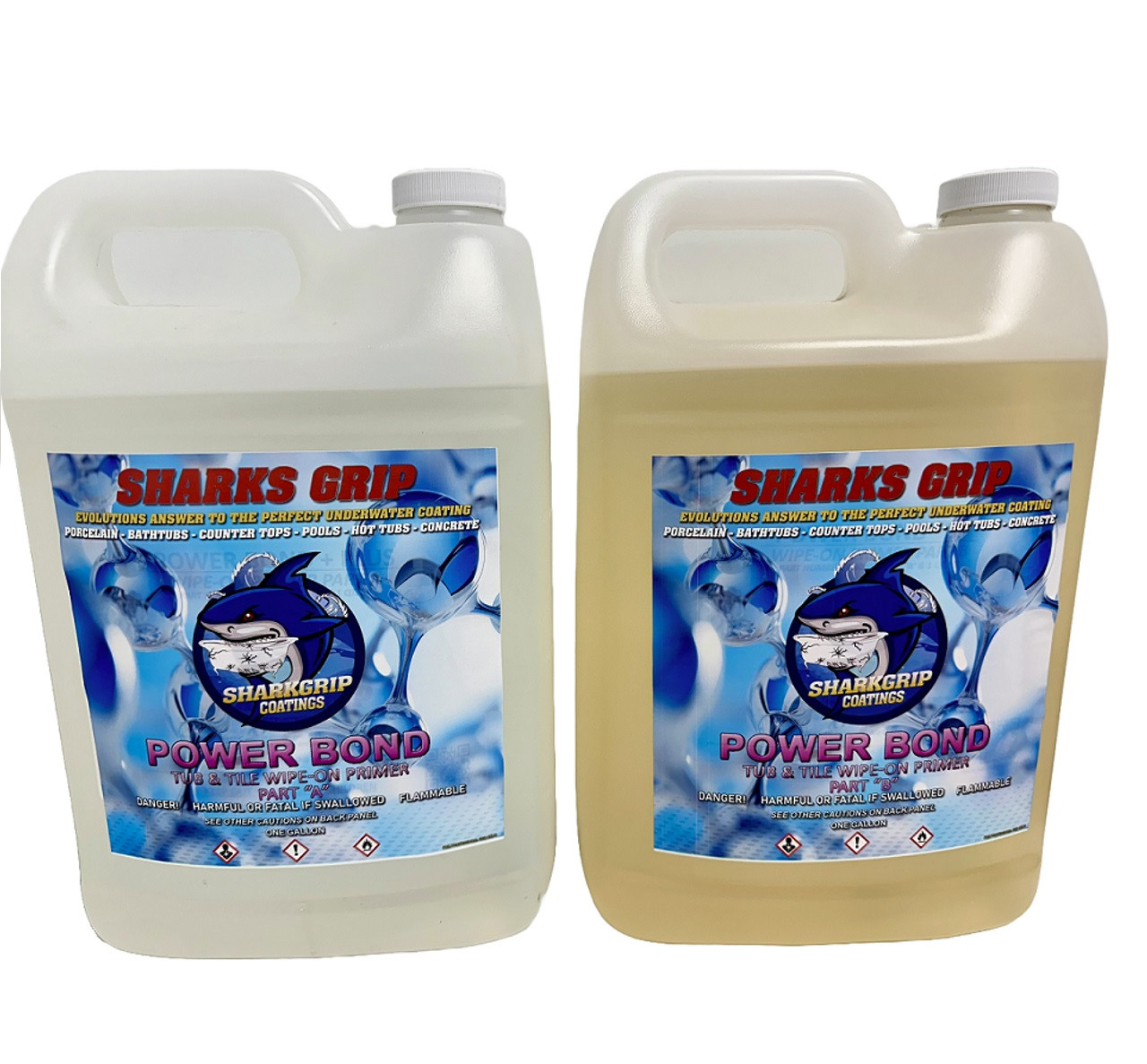
6. Flaking
What It Looks Like: Small, brittle chips are often breaking off from edges, drain areas, or seams.
Why It Happens:
- The underlying surface is brittle, aged, or improperly bonded.
- The existing coating was never made for bathtubs—commonly seen with Cardinal or other industrial finishes.
- Coating lacks flex and cracks under heat expansion or daily use.
Refinisher Warning: Flaking is a red flag that your base layer may have been a generic topcoat from a local paint store, not a true refinishing product. These coatings often have low elongation and high stiffness, not suitable for dynamic, wet environments like bathtubs.
Can You Apply a Tie-Coat or Do You Need to Strip?
Refinishers often face this choice: Strip everything to porcelain, or bond over what’s there? Here's how to make the call.
? Step-by-Step: Can a Tie-Coat Be Used?
- ✅ Test Surface Integrity: Use Crosshatch Tape Test. If >10% lifts: strip it.
- ✅ Check for Bubbling or Softness: If the base moves under a fingernail, strip it.
- ✅ Test for Contaminants: Use SWAT wipe. If oily or discolored, clean or strip.
- ✅ Water Break Test: Mist water. If it beads: contamination present.
- ✅ Identify Coating Type: Acetone wipe test to check chemical resistance.
- ✅ Apply Spot Test: 6x6" test panel before committing to full refinish.
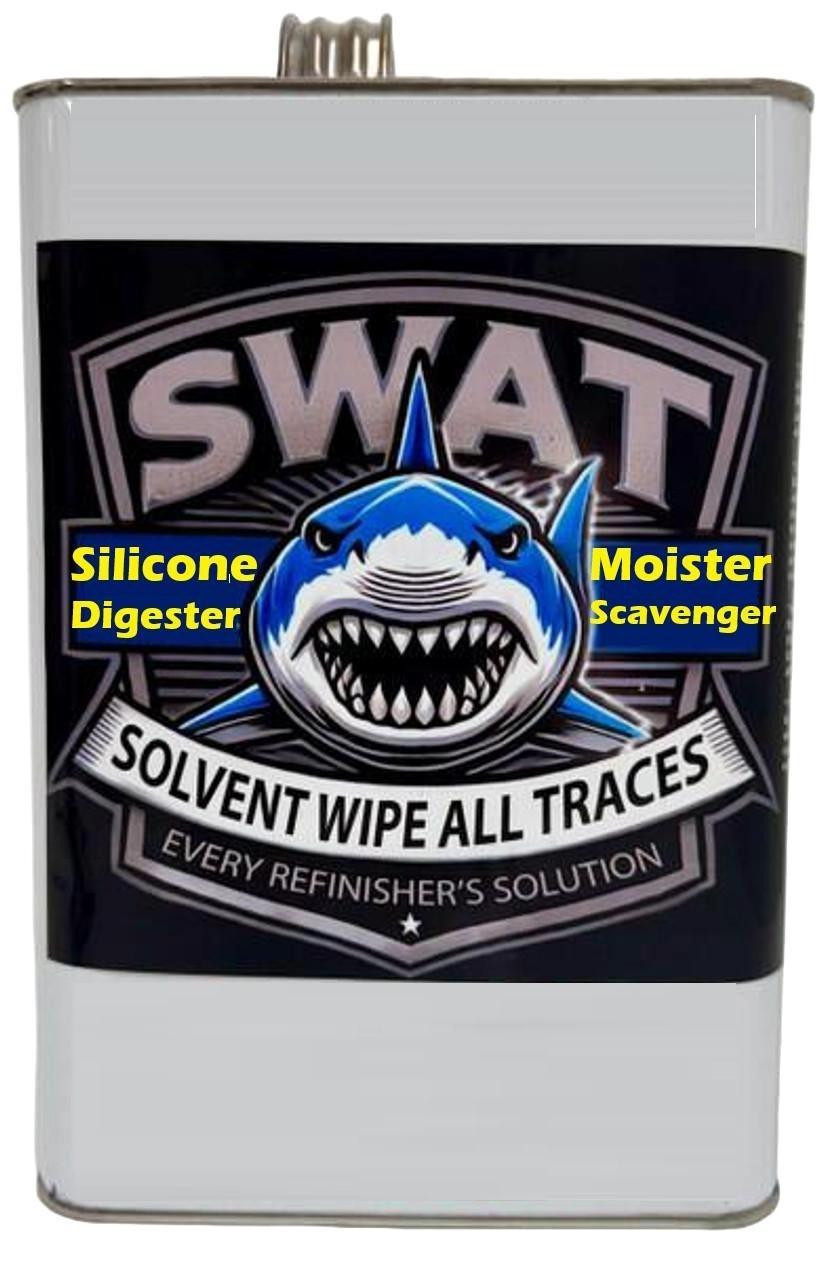
Final Thoughts: Don’t Skip the Science
Many refinishers try to cut corners to save time, but skipping surface prep or bonding steps is a gamble that almost always ends in a redo. Especially when you’re working over non-bathtub-specific coatings, like those found at industrial suppliers.
Use the right chemistry, the right testing, and the right system. Whether it’s Power Bond, Bull Shark, or Epoxy Primer, a proper tie-coat system is your armor when stripping isn’t feasible.
- ✅ Always test before you trust.
- ✅ Don’t assume every coating can be refinished over.
- ? When in doubt—strip it out.
Your customers don’t care how fast you finished a job. They care that it lasts.
Recent Posts
-
SCENTRALOCK - VOC - ISOCYANATE and SOLVENT SUPRRESSOR - ODOR ELMINATOR
What’s Really Happening When You Add ScentraLock™ When you add ScentraLock™ to yo …Apr 29th 2025 -
“Professional Refinishers: Are You Still Spraying Over Old Junk?
Understanding Common Coating Failures in the Bathtub Refinishing Industry And How to Deter …Apr 21st 2025 -
Melt Down vs. EZ Flow: What's the Difference?
Melt Down vs. EZ Flow: What's the Difference? Refinishers often ask us to explain the diffe …Apr 2nd 2025